By Milagros Watts
Why is Digital Color Communication Important?
Every business is faced with the challenge of getting the right product in front of customers at the right moment. This is especially true in the paint, coatings, plastics and textile industries—ones that the team at Datacolor is very familiar with. Rapid changes in color preferences mean companies must keep pace with the ever-evolving trends, without sacrificing precision. There’s no doubt about it: digital color communication can streamline the color development cycle and accelerate speed to market.
Yet, the digital color communication process is only as sound as the color data upon which the process is built. The key to effective color communication is controlling the factors that can interfere with accurate color data.
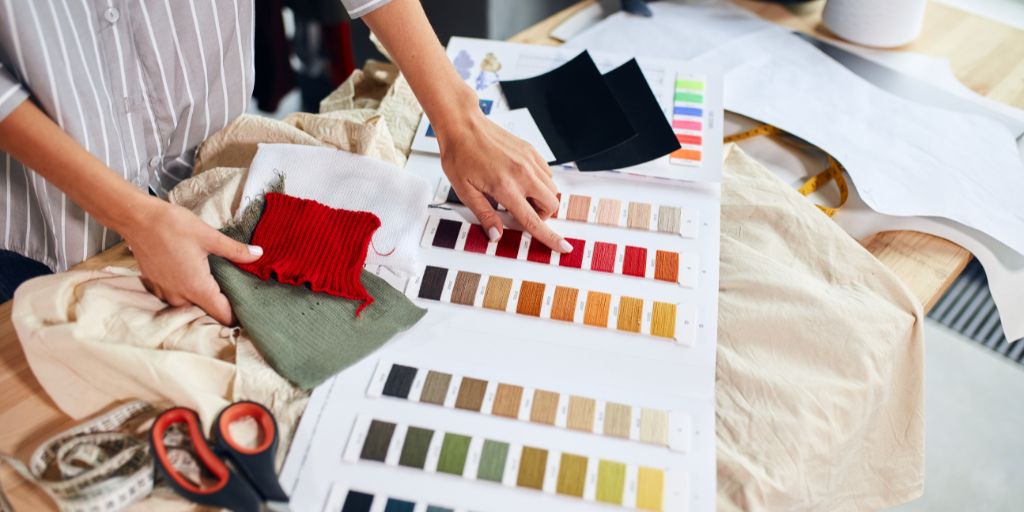
The Importance of Accurate Color Data
In a world with millions of different hues, the process of measuring color is inherently prone to variation. When that variation goes unchecked, even digital color data can fall prey to costly misunderstandings and crippling delays in the development cycle. To ensure confidence in the quality of the digital color data being exchanged, the sources of any variation in the measurement process must be identified and controlled. Here are the steps that must happen for successful digital color communication.
Step 1: Identify a standard for color matching
The first step of any successful color communication process is identifying a standard for color matching. The original source of inspiration might be a swatch of fabric, a chip of paint or a hue developed on a monitor. No matter how the color originates, the target must bbe communicated accurately, across the supply chain,all the way to the final product. Identifying a standard that can be accurately produced in the intended substrate and process sets the stage for accurate color matching.
Step 2: Represent a standard digitally
Once a standard is established, it can be represented digitally, opening the door for clear communication from design to execution—and every stop along the way. A digital standard is a set of numbers, or spectral reflectance values, each of which corresponds to the amount of light that reflects off the target color at different wavelengths relative to a perfect white. The way a color interacts with light gives us a numerical definition of that color, which can be communicated across the supply chain and recreated when color is applied to the final product.
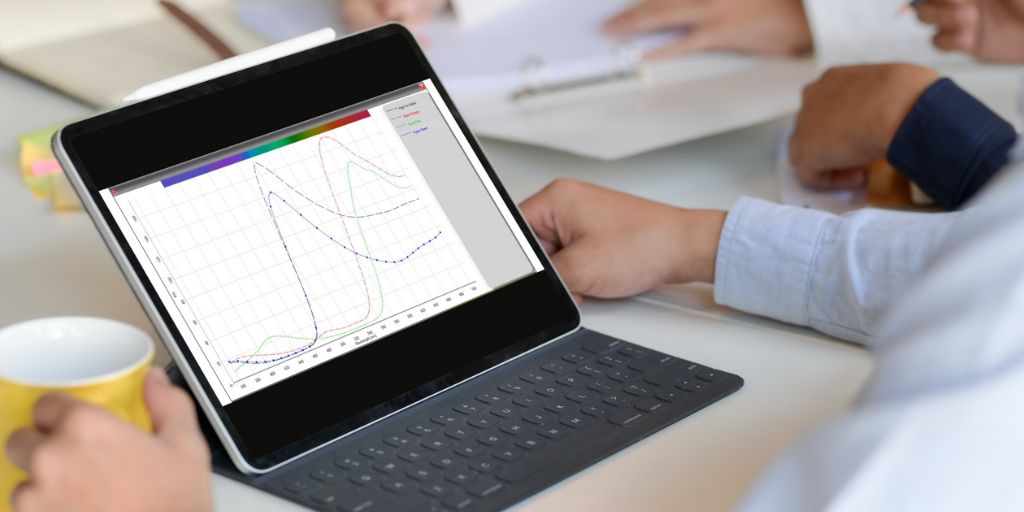
Step 3: Know how to achieve precise color measurements
Homing in on spectral reflectance requires a precise and repeatable measurement technique. The Datacolor 1000 Spectrophotometer is a state-of-the-art instrument that delivers reliable color measurement data that can be repeated.
For optimal performance, the properties of the sample must be taken into account. In textile fabrics for instance, ensuring the sample is folded until opaque is critical because any light that passes through the material will reflect off other surfaces and produce misleading reflectance data.
Using the spectrophotometer’s largest aperture size will minimize the variation across the sample, allowing users to define a color in terms of its numerical value—and then repeat the measurement to ensure accuracy.
That numerical value, then becomes universal as it instantly reaches the inboxes of everyone involved in bringing the color to life, whether it’s on a garment or a paint brush.
Central to the spectrophotometer’s ability to accurately capture spectral data and communicate it to various touchpoints along the supply chain is the concept of inter-instrument agreement. With all of the people involved in getting color right at a company separated by oceans and continents, measurement data must be reliable and repeatable, not only on the original instrument, but on other instruments.
Step 4: Match the Color
Once the physical color standard has been measured and translated into a digital color, suppliers use formulation software to build the desired color specifications. Datacolor Match Textile, aptly named for the textile industry, and Datacolor Match Pigment, designed for several industries, including paint, pigment, plastics, leather, inks and cosmetics, are sophisticated software solutions that formulate color and control for typical challenges that can derail the quest for accuracy.
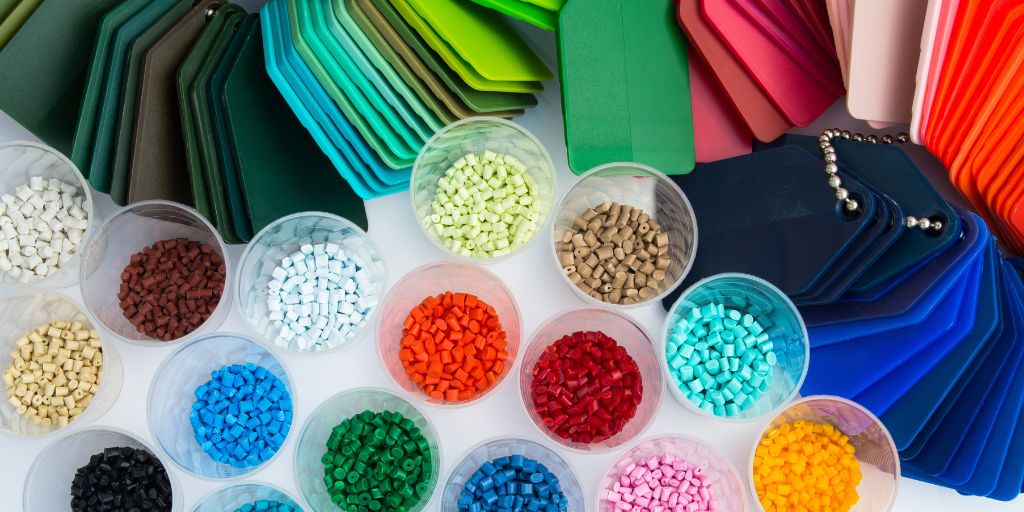
Understanding the Role of Metamerism
Chief among those challenges is metamerism, a phenomenon that occurs when two colors appear to match perfectly under one lighting condition, but no longer match under different lighting. Datacolor’s matching software ensures an accurate color match that accounts for illuminants selected during formulation, which means different elements of a product—from textile fabrics for car interiors—will coordinate when the final product is assembled, no matter the lighting.
How to Share Color Data Across the Supply Chain
The key to successfully executing color is the ability to seamlessly share reliable digital color data with all the players involved during each step of the development cycle. Datacolor’s suite of color measurement instruments and formulation software solutions give customer the tools to avoid costly missteps, accelerate the production cycle and deliver precise color time and time again.
Still have questions about effective digital color communication? Contact your Datacolor representative or ask us a question here.